Moog Aircraft Group obniża koszty osprzętu i skraca czas realizacji zamówień dzięki drukowi 3D w technologii FDM
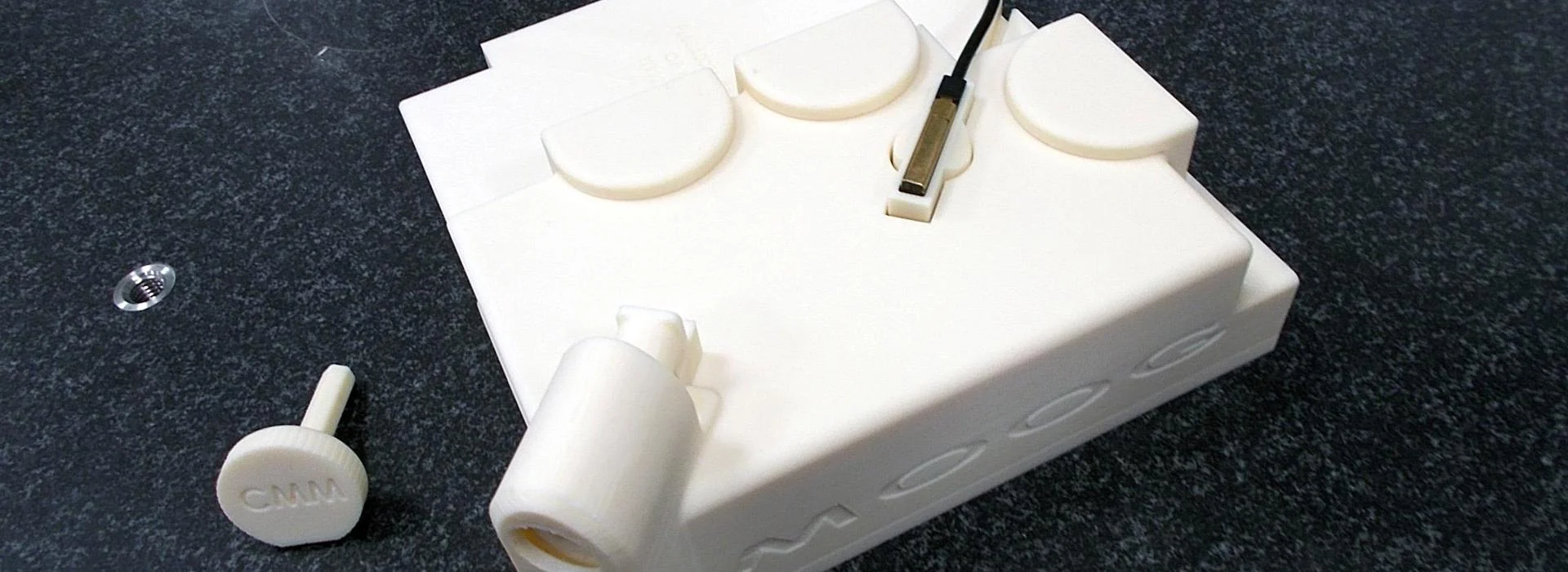
Możliwość wypróbowania pomysłu projektowego, przetestowania go i odpowiedniego przeprojektowania w ciągu kilku godzin, a nie tygodni, pozwoliła poprawić ciągłość pracy i zmniejszyć liczbę uszkodzeń spowodowanych ręcznym przenoszeniem w trakcie procesów produkcyjnych.
Moog Aircraft Group (Moog) dostarcza rozwiązania inżynieryjne i zaawansowane technologie na rynek samolotów wojskowych od momentu swojego powstania w latach 50. ubiegłego wieku. Obecnie firma jest uznawana za światowego lidera w produkcji zaawansowanych rozwiązań dla samolotów o najwyższych osiągach na świecie.
Wybór bardziej wydajnych metod
Zakład firmy Moog w Wolverhampton zdecydował się na inwestycję w poprawę swoich wewnętrznych możliwości w zakresie kontroli CMM. Obejmowało to użycie dedykowanego oprzyrządowania dla każdej operacji kontroli obrabianej części. Tradycyjnie, oprzyrządowanie do mocowania i osiowania części było zlecane zewnętrznym dostawcom, gdzie oprzyrządowanie było wykonane ze stali narzędziowej.
Biorąc pod uwagę liczbę urządzeń zaangażowanych w projekt usprawnienia współrzędnościowej maszyny pomiarowej, oznaczałoby to znaczne wydatki.
James Stuart-Young, kierownik ds. inżynierii produkcji w Moog Aircraft Group
„Ponadto proces outsourcingu zawsze wiązał się z czasem realizacji wynoszącym od czterech do sześciu tygodni od wydania rysunku do otrzymania gotowego oprzyrządowania. Po przeprowadzeniu analizy kosztów i korzyści, oceniliśmy sposoby produkcji tych elementów we własnym zakresie. Celem było skrócenie planowanego czas realizacji elementów. Druk 3D okazał się najbardziej stosowną w tym wypadku metodą wytwarzania ze względu na szybkość i niskie koszty części”.
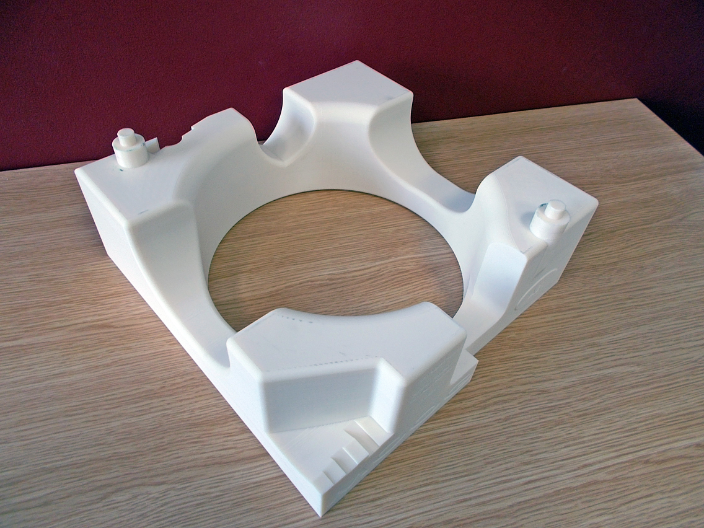
Firma Moog dokonała przeglądu wielu opcji podczas fazy oceny i wybrała drukarkę 3D Stratasys Fortus 380mc, ponieważ spełniała ona wszystkie wymagane standardy techniczne. „Fortus 380mc w serii prób wytworzył najbardziej stabilną część dla procesu kontroli jakości” – powiedział Stuart-Young. „Co więcej obszar roboczy i materiały dostępne do druku 3D spełniły nasze potrzeby, a cena mieściła się w naszym budżecie”.
Droga do potrzebnych w procesie sprawdzianów
System Fortus w firmie Moog osiągnął niemal pełne obłożenie w produkcji oprzyrządowania do kontroli CMM. Technologia CAD umożliwia modelowanie złożonych kształtów, dzięki czemu części mogą być zorientowane w sposób korzystny dla różnych cech w jednym ustawieniu.
W odniesieniu do wyboru materiału, Stuart-Young powiedział: „Istnieje potrzeba, aby oprawy były odporne na temperaturę i światło ultrafioletowe, co skłoniło nas do wyboru ASA w odcieniu kości słoniowej”. ASA to termoplastyczny materiał produkcyjny odporny na promieniowanie UV, który zapewnia wytrzymałość i wysokiej jakości wykończenie powierzchni.
Pomyśleliśmy, że przyda ci się nasz poradnik
Porównujemy w nim drukarki, żeby ułatwić ci podjęcie decyzji
o wdrożeniu druku 3D dopasowanego do twojej firmy.
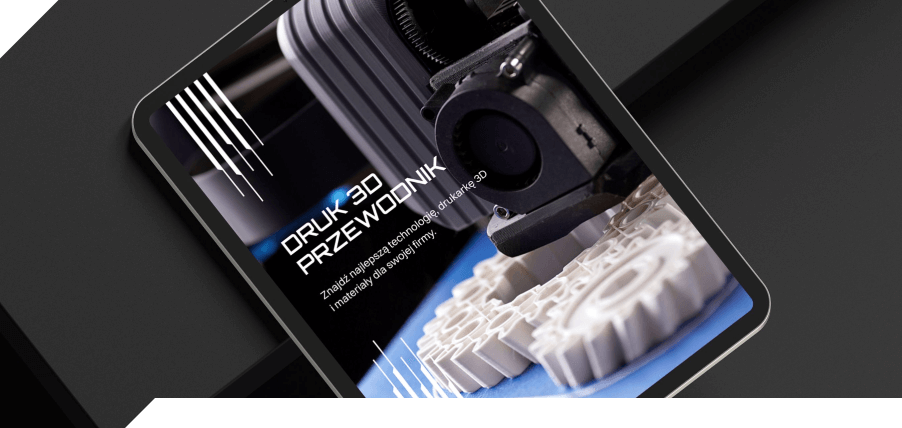
Z myślą o tym stworzyliśmy “Porównanie drukarek 3D. Uniwersalny przewodnik użytkownika”.
Nasz przewodnik pomoże ci w procesie decyzyjnym. To użyteczny materiał, który będziesz mógł przedstawić na zarządzie lub przed komitetem zakupowym. Pomaga ocenić technologie i drukarki 3D pod względem szeregu przydatnych kryteriów.
Co znajdę w poradniku?
- Opisy cech charakterystycznych technologii druku 3D.
- Porównanie drukarek 3D różnych producentów według segmentów rynku.
- Porównanie technologii druku 3D.
- Case study zakupu drukarki 3D.
Od outsourcingu do insourcingu
Przed wprowadzeniem druku 3D firma Moog zlecała produkcję wszystkich narzędzi i osprzętu podwykonawcom.
Zdolność do produkcji we własnym zakresie pozwoliła nam odzyskać kontrolę nad ustalaniem priorytetów produkcji zgodnie z wymaganiami programu klienta.
James Stuart-Young, kierownik ds. inżynierii produkcji w Moog Aircraft Group
„Czasy druku różnią się w zależności od zakresu drukowanych części, ale w przypadku uchwytów CMM jest to około 20 godzin. Co więcej, oprzyrządowanie, które w przeszłości kosztowało ponad 2000 funtów, można teraz wykonać za kilkaset funtów”.
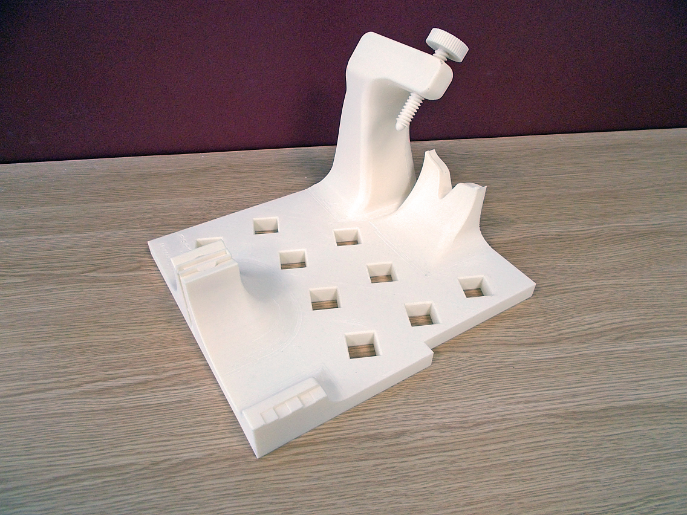
Automatyczne usuwanie podpór
Aby uzyskać jeszcze większą wydajność prototypowania i produkcji, Moog wykorzystuje rozpuszczalne materiały podporowe Stratasys SR-30 i SR-100 do automatycznego usuwania bez użycia rąk.
„Umieszczamy wydrukowane części w naszym zbiorniku czyszczącym, aby rozpuścić rozpuszczalny materiał podporowy” – pokazuje Stuart Young. „Oprzyrządowanie jest następnie przechowywane w pobliżu maszyn CMM w celu ułatwienia dostępu”.
Obecnie Fortus 380mc działa w firmie Moog prawie 24 godziny na dobę, siedem dni w tygodniu. Ponadto działy takie jak Montaż i Testowanie oraz Inżynieria Rozwoju zdały sobie sprawę z oszczędności czasu przy tworzeniu złożonych narzędzi i osprzętu. Korzystając z drukarki 3D, inżynierowie są w stanie wdrożyć różne grubości warstw, aby odpowiednio zmienić czas drukowania.
„Możliwość wypróbowania pomysłu na projekt, przetestowania go i odpowiedniego przeprojektowania w ciągu kilku godzin, a nie tygodni, pozwoliła nam poprawić ciągłość pracy i zmniejszyć liczbę uszkodzeń spowodowanych ręczną obsługą w całym procesie produkcyjnym” – podsumował Stuart-Young.
Podsumowanie
Moog Aircraft Group z powodzeniem wprowadziło druk 3D jako sposób na obniżenie kosztów i skrócenie czasu produkcji uchwytów inspekcyjnych. Tradycyjnie wykonywane ze stali narzędziowej uchwyty były zamawiane zewnętrznie, co wiązało się z dużymi kosztami i długim czasem realizacji.
W wyniku analizy kosztów i korzyści firma zdecydowała się na zastosowanie drukarki Stratasys Fortus 380mc, która zapewniła stabilność produktów, elastyczność projektowania i zgodność z wymaganiami technicznymi. Dzięki wykorzystaniu termoplastu ASA jako materiału, uchwyty są odporne na promieniowanie UV i zmienne temperatury, co jest kluczowe w zastosowaniach przemysłowych.
Produkując uchwyty wewnętrznie, Moog zmniejszył koszty z tysięcy do setek funtów za sztukę oraz skrócił czas realizacji z tygodni do godzin. Dodatkowo dzięki automatycznemu usuwaniu podpór i elastycznemu projektowaniu CAD firma poprawiła procesy produkcji, minimalizując uszkodzenia i zwiększając wydajność.
Wdrożenie druku 3D umożliwiło także szybsze testowanie i modyfikowanie projektów, co znacznie usprawniło realizację wymagań klientów.
Źródło: materiały Stratasys
Prześlij formularz, nasz konsultant skontaktuje się z tobą w ciągu 15 minut
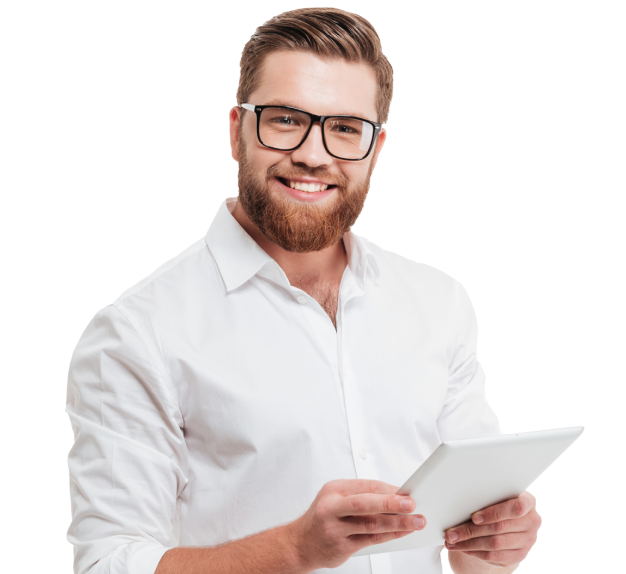