Szybkie prototypowanie i produkcja narzędzi w Marshall Aerospace
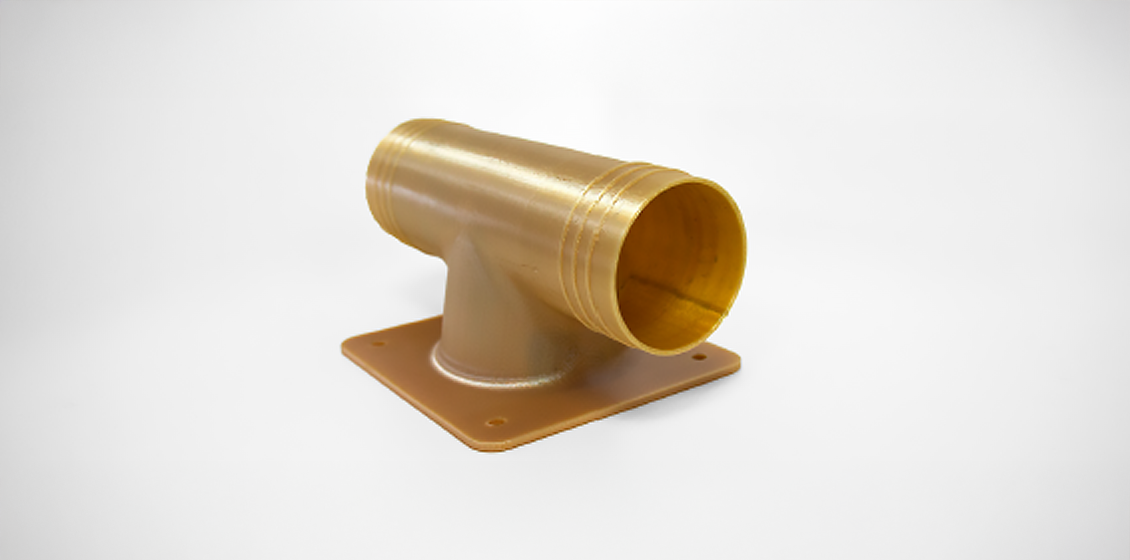
Przemysł zbrojeniowy z powodzeniem wykorzystuje technologie przyrostowe, a siły zbrojne kolejnych państw wprowadzają je do codziennej pracy inżynierów. W wielu przypadkach druk 3D pozwala na szybkie prototypowanie złożonych części. Marshall Aerospace, brytyjski lider w dziedzinie lotnictwa i obronności, postawiła na druk 3D, aby sprostać wyzwaniom związanym z produkcją lekkich, wytrzymałych i certyfikowanych komponentów.
Ich współpraca z firmą Stratasys pozwoliła na przyspieszenie procesów projektowych oraz obniżenie kosztów produkcji. Dzięki wykorzystaniu drukarek Fortus 450mc i F370 firma osiągnęła przewagę technologiczną. Oto jak druk 3D zmienia oblicze przemysłu zbrojeniowego i pomaga Marshall Aerospace utrzymać ciągłość realizacji zamówień.
O firmie
Marshall Aerospace
Marshall Aerospace and Defence Group, z siedzibą w Wielkiej Brytanii, to jedna z największych prywatnych firm z sektora lotniczo-obronnego. Specjalizuje się w modyfikacji i konwersji samolotów wojskowych, cywilnych i biznesowych, a także w projektowaniu pojazdów wojskowych oraz produkcji schronień.
Firma działa globalnie, dostarczając innowacyjne rozwiązania zarówno na lądzie, morzu, jak i w powietrzu. W portfolio firmy znajdują się także usługi związane z modernizacją systemów awioniki, co czyni Marshall Aerospace kluczowym graczem w sektorze obronnym.
Aby sprostać wymaganiom rynku, firma inwestuje w najnowsze technologie, w tym zaawansowany druk 3D. Współpracując ze Stratasys, Marshall Aerospace zyskało możliwość wdrażania szybkiego prototypowania oraz produkcji narzędzi i komponentów, które spełniają normy branżowe.
Dzięki temu firma minimalizuje koszty i czas realizacji projektów. Nowoczesne podejście do projektowania pozwala Marshall Aerospace utrzymać przewagę konkurencyjną.
Jak mówi Chris Botting, inżynier ds. materiałów:
Dzięki technologii druku 3D możemy tworzyć rozwiązania w sposób, który wcześniej był niemożliwy.
Chris Botting, inżynier ds. materiałów
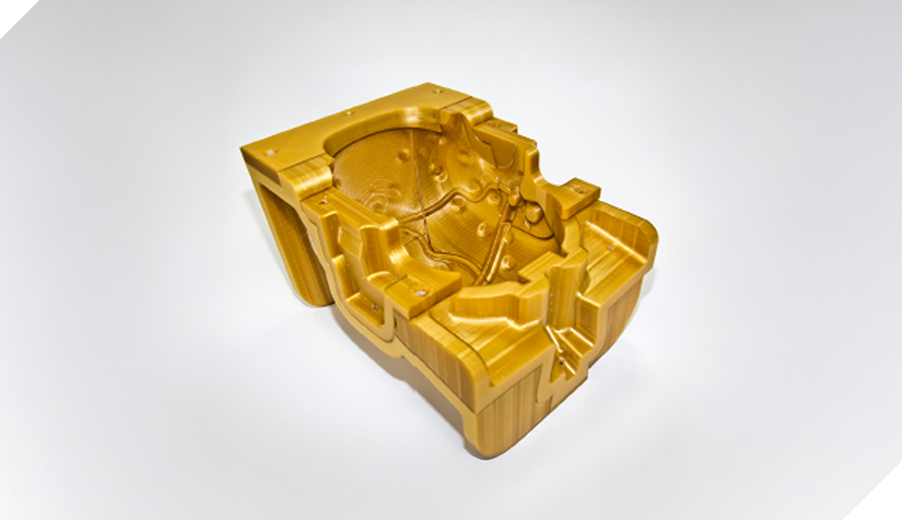
Wyzwanie
Zastępstwo dla aluminium
Marshall Aerospace musiało stawić czoła problemom związanym z tradycyjnym podejściem do prototypowania, które wymagało użycia aluminium jako materiału bazowego. Proces ten był czasochłonny i kosztowny, a dodatkowo ograniczał elastyczność projektową.
Kluczowym wyzwaniem było wytwarzanie lekkich, ale wytrzymałych części spełniających normy lotnicze, takie jak odporność na płomienie, dym i toksyczność (EASA).
Przykładowymi komponentami były adaptery kanałów powietrznych, które dostarczają powietrze do chłodzenia awioniki na ziemi, oraz narzędzia formujące do produkcji elementów kompozytowych. Części te musiały być nie tylko funkcjonalne, ale także dostosowane do warunków pracy w przemyśle lotniczym.
Kolejnym wyzwaniem była potrzeba szybkiego tworzenia prototypów złożonych komponentów bez obniżania ich jakości. Tradycyjne metody powodowały opóźnienia w realizacji projektów, co wpływało na koszty i terminy dostaw. Firma musiała znaleźć sposób na zwiększenie responsywności wobec potrzeb klientów i jednocześnie zoptymalizować koszty produkcji.
Jak podkreśla Stuart Dean, kierownik projektowy w Marshall Land Systems:
W dziale Land Systems musimy tworzyć prototypy niezwykle skomplikowanych części, unikając konieczności obsługi skomplikowanych maszyn i tworzenia długich procesów.
Stuart Dean, kierownik projektowy w Marshall Land Systems
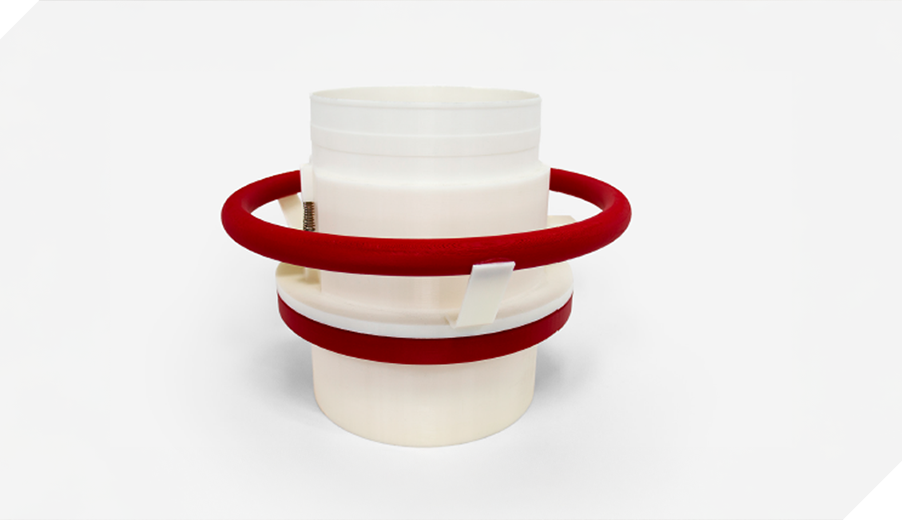
Rozwiązanie
Drukarki Stratasys w technologii FDM
Marshall Aerospace wdrożyła technologię druku 3D FDM (Fused Deposition Modeling), która pozwala na szybkie i efektywne tworzenie prototypów oraz narzędzi. Firma korzysta z drukarek Stratasys Fortus 450mc i F370, które umożliwiają produkcję komponentów z materiałów takich jak ULTEM™ 9085 i Nylon 12.
ULTEM™ 9085 to wysokowydajny materiał termoplastyczny, odporny na wysokie temperatury i chemikalia, a także zgodny z wymogami lotniczymi. Dzięki drukarce 3D Stratasys Fortus 450mc firma mogła w ciągu zaledwie kilku godzin stworzyć prototyp kanału powietrznego, który następnie został certyfikowany do użytku w lotnictwie.
Drukarka 3D Stratasys F370 była wykorzystywana do produkcji narzędzi formujących oraz innych narzędzi warsztatowych w mniej niż 24 godziny. Wykorzystanie tych technologii zmniejszyło zależność firmy od zewnętrznych dostawców i wyeliminowało wąskie gardła w produkcji.
Co więcej elastyczność materiałowa oferowana przez drukarki Stratasys pozwoliła inżynierom wybrać odpowiedni materiał do każdej aplikacji.
„Dzięki tym drukarkom zyskaliśmy nie tylko oszczędność czasu, ale również pełną kontrolę nad procesem wytwarzania”, podkreśla Chris Botting.
Firma wykorzystała druk 3D także do produkcji krótkoseryjnych zindywidualizowanych narzędzi produkcyjnych, co było niemożliwe przy tradycyjnych metodach.
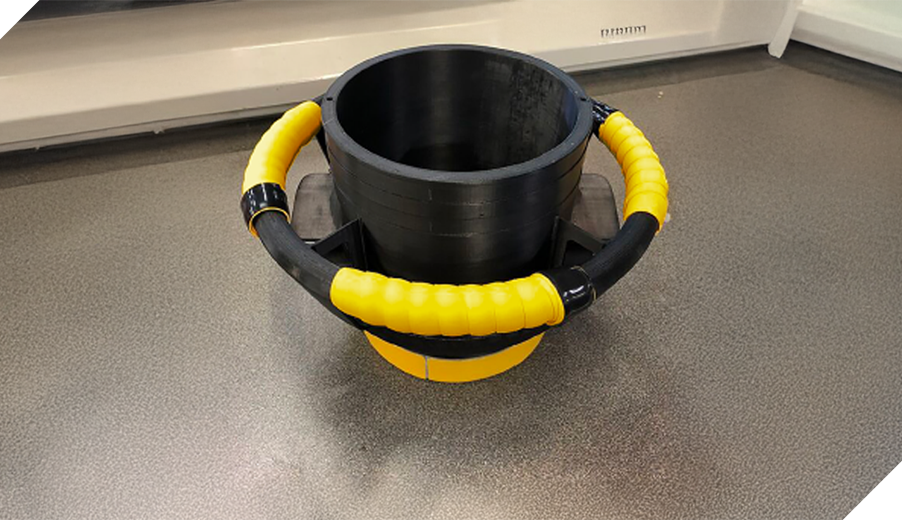
Pomyśleliśmy, że przyda ci się nasz poradnik
Porównujemy w nim drukarki, żeby ułatwić ci podjęcie decyzji
o wdrożeniu druku 3D dopasowanego do twojej firmy.
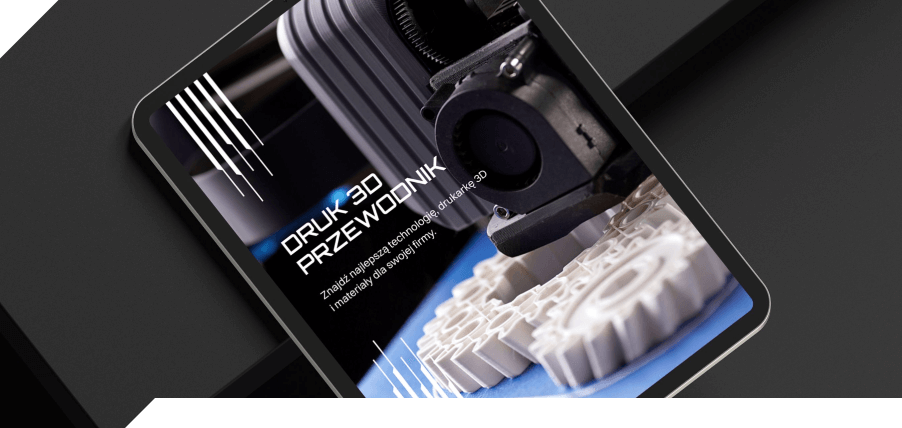
Z myślą o tym stworzyliśmy “Porównanie drukarek 3D. Uniwersalny przewodnik użytkownika”.
Nasz przewodnik pomoże ci w procesie decyzyjnym. To użyteczny materiał, który będziesz mógł przedstawić na zarządzie lub przed komitetem zakupowym. Pomaga ocenić technologie i drukarki 3D pod względem szeregu przydatnych kryteriów.
Co znajdę w poradniku?
- Opisy cech charakterystycznych technologii druku 3D.
- Porównanie drukarek 3D różnych producentów według segmentów rynku.
- Porównanie technologii druku 3D.
- Case study zakupu drukarki 3D.
Wyniki
Elementy z Nylonu 12
Adaptery kanałów powietrznych drukowane w materiale Nylon 12 okazały się o 63% lżejsze od ich aluminiowych odpowiedników. Tym samym obniżono końcowe koszty produkcji.
ULTEM™ 9085 pozwolił na produkcję części zgodnych z normami lotniczymi, co otworzyło nowe możliwości w zastosowaniach lotniczych. Części mogły być certyfikowane do użytku w lotnictwie komercyjnym i wojskowym.
Narzędzia produkcyjne, takie jak szablony wiercenia, formy kompozytowe i narzędzia montażowe, były dostarczane inżynierom w mniej niż 24 godziny, co przyspieszyło cały proces projektowania i produkcji. Marshall Aerospace była w stanie szybko reagować na potrzeby klientów i realizować złożone projekty w krótszym czasie.
Jak zauważa Chris Botting:
FDM to technologia, która zmieniła sposób, w jaki projektujemy i produkujemy nasze komponenty. Patrząc w przyszłość, widzimy ogromny potencjał w dalszym rozwijaniu tej technologii w branży lotniczo-obronnej.
Chris Botting, inżynier ds. materiałów
Przed zastosowaniem drukarek 3D od Stratasys wiele prototypów i części było zamawiane u poddostawców metodą frezowania bądź formowania wtryskowego.
Niemożliwa była optymalizacja ich wagi. Wiązało się to również z dłuższymi czasami od projektu do zastosowania.
Zwrot z inwestycji
Dzięki technologiom addytywnym firma stworzyła lżejsze adaptery kanałów powietrznych i przyspieszyła prototypowanie w dziale badań i rozwoju.
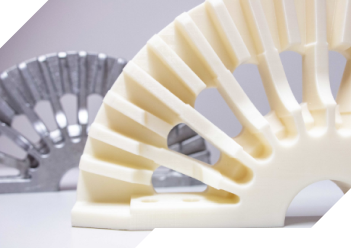
Prześlij formularz, nasz konsultant skontaktuje się z tobą w ciągu 15 minut
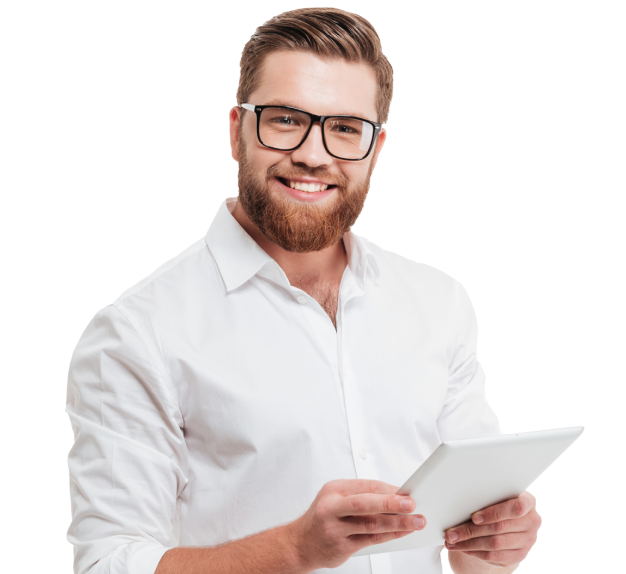