Druk 3D wkładek do formowania wtryskowego
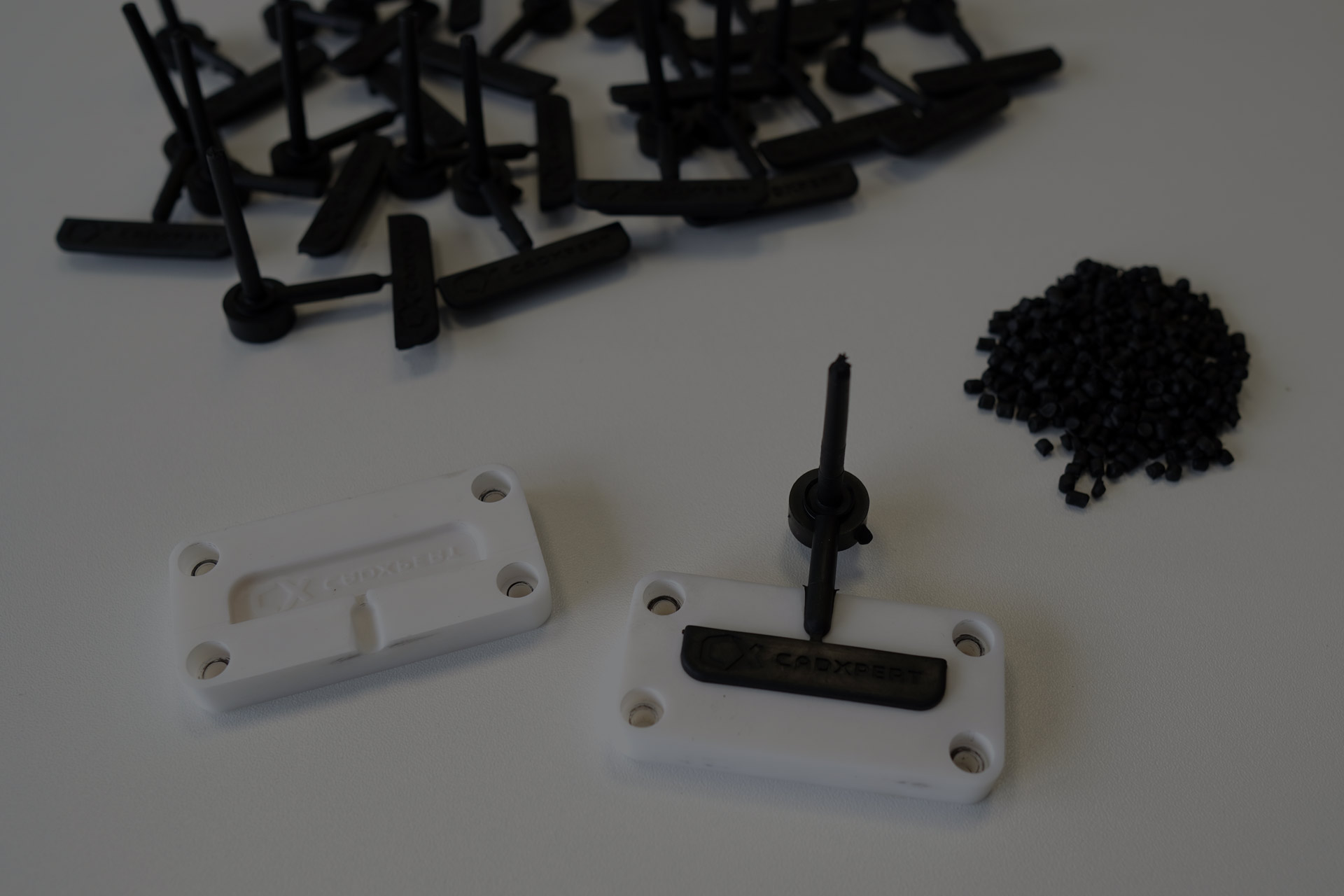
30 zł zamiast 15 000 zł – porównanie kosztów wykonania wkładki do formowania wtryskowego przedstawia poziom oszczędności, jakie niesie wdrożenie druku 3D na produkcji. Firma 3DeM z Wieliczki k. Krakowa przeprowadziła testy wytrzymałości narzędzi wydrukowanych na drukarkach 3D Formlabs Form 3 w technologii SLA / LFS.
Firma 3DeM świadczy usługi produkcji seryjnej: frezowanie CNC, toczenie, druk 3D, wycinanie laserowe, spawanie.
„W naszej pracy postawiliśmy sobie za cel aby w sposób kompleksowy rozwiązywać problemy związane z wytwarzaniem i produkcją. Wykorzystując kreatywność, specjalistyczną wiedzę techniczną tworzymy nieszablonowe rozwiązania dla przemysłu” – czytamy na stronie firmy.
Jedną z innowacji, jakie wprowadziła firma było wykorzystanie technologii druku 3D do produkcji wkładek do formowania wtryskowego.
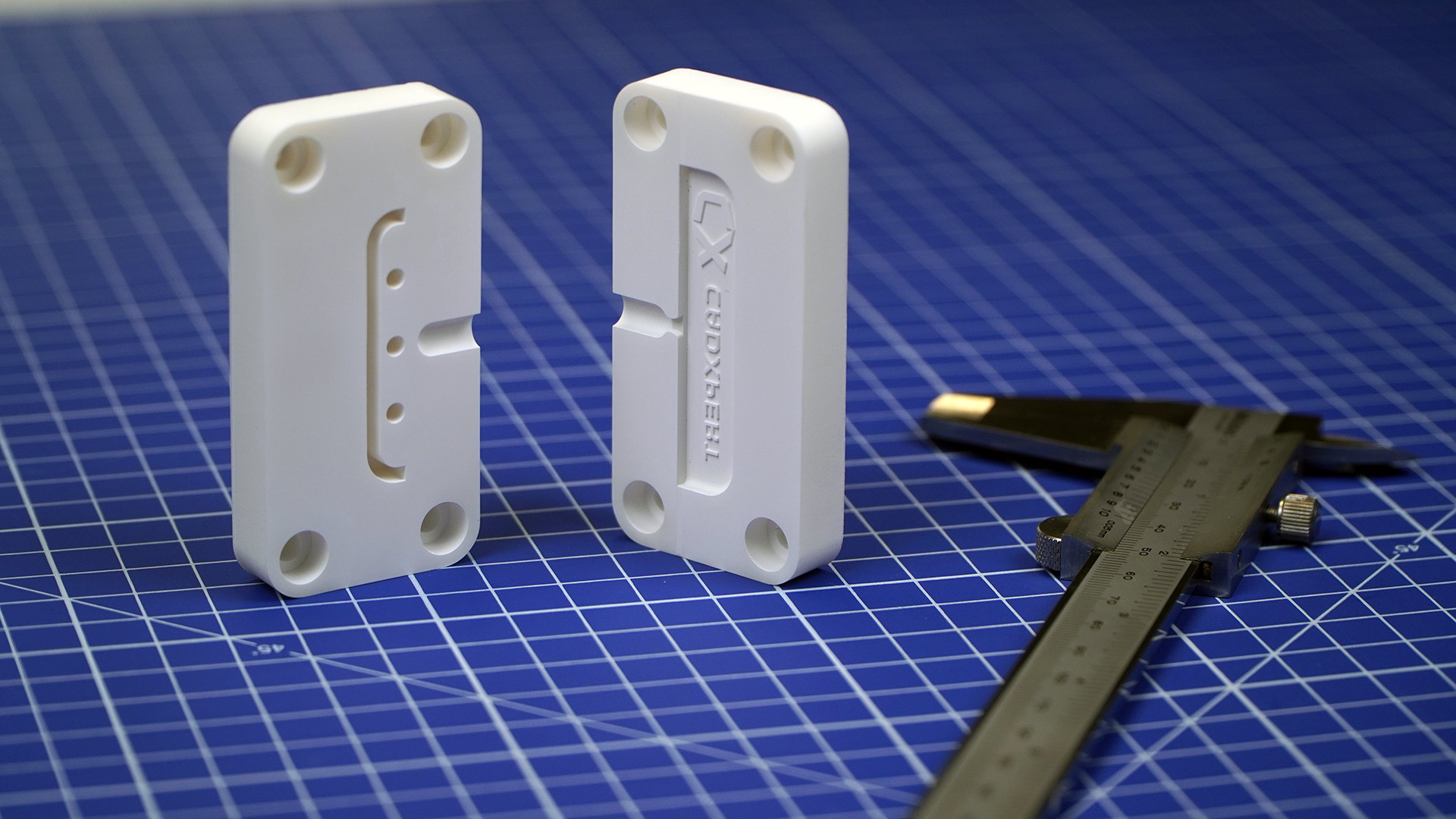
4 Korzyści zastosowania technologii druku 3D w produkcji wkładek do formowania wtryskowego
- Bezkonkurencyjna oszczędność czasu i kosztów w porównaniu do konwencjonalnych metod.
- Możliwość weryfikacji projektu wkładki przed złożeniem zamówienia na formę z metalu.
- Możliwość testowania produktu na docelowo wtryskiwanym materiale przed rozpoczęciem produkcji masowej.
- Możliwość przyjmowania zleceń na krótkie serie produkcyjne.
Projekt #1 – Zaślepka do profilu aluminiowego
Dla jednego ze swoich klientów firma wydrukowała wkładkę na drukarce 3D Formlabs Form 3 z żywicy High Temp. Do wtrysku użyto materiału TPU (docelowy materiał zamówiony przez klienta) oraz dla testów wytrzymałościowych – sztywny materiał HDPE.
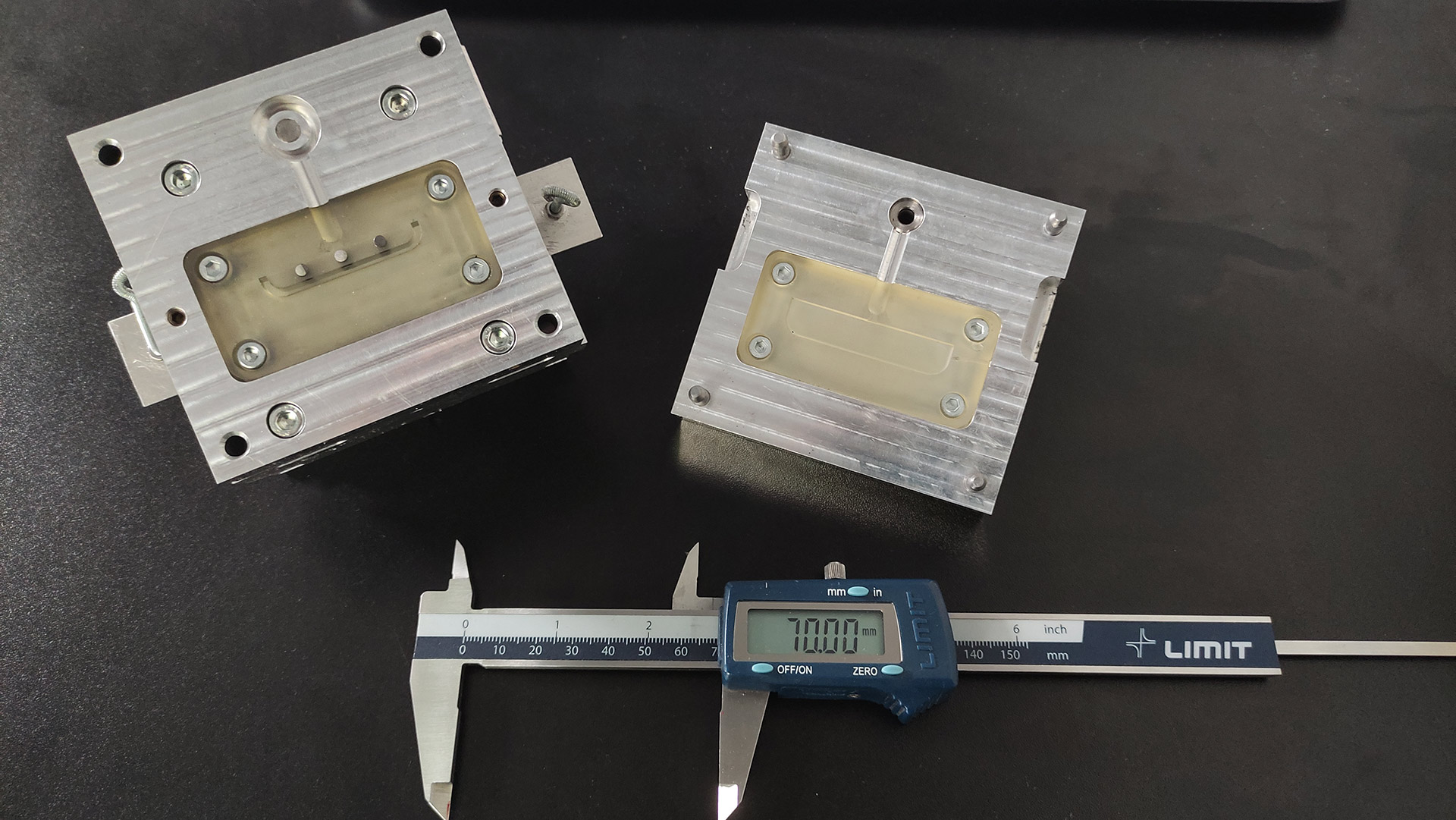
PARAMETRY WTRYSKU
Materiał wkładki — żywica Formlabs High Temp
Materiał wtrysku — TPU oraz HDPE
Temperatura wtrysku TPU — 145-150 °C.
Temperatura wtrysku HDPE — 150 °C
Siła zwarcia formy — ok. 10-15 T
Liczba wtrysków — łącznie ok. 150 sztuk (100-120 TPU i 30 HDPE)
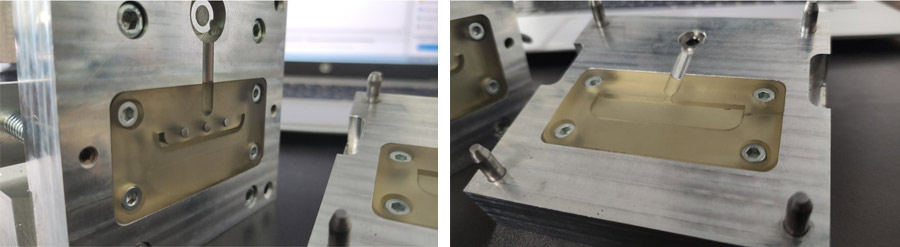
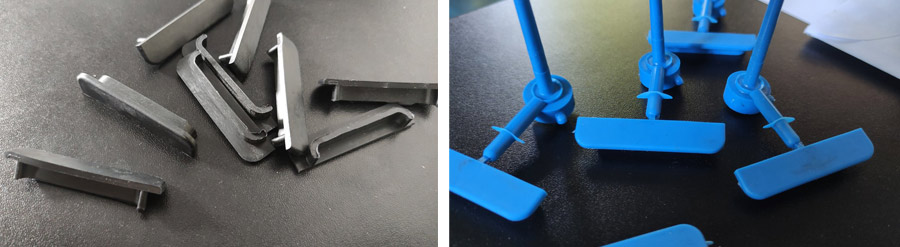
Pomyśleliśmy, że przyda ci się nasz poradnik
Porównujemy w nim drukarki, żeby ułatwić ci podjęcie decyzji
o wdrożeniu druku 3D dopasowanego do twojej firmy.
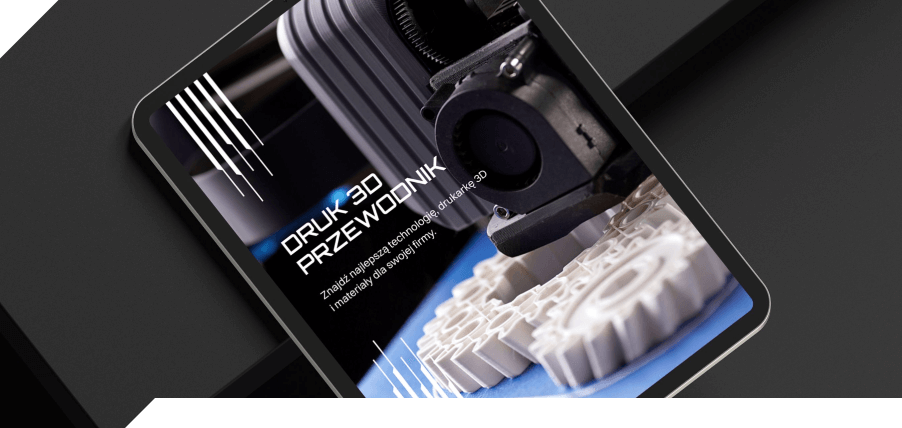
Z myślą o tym stworzyliśmy “Porównanie drukarek 3D. Uniwersalny przewodnik użytkownika”.
Nasz przewodnik pomoże ci w procesie decyzyjnym. To użyteczny materiał, który będziesz mógł przedstawić na zarządzie lub przed komitetem zakupowym. Pomaga ocenić technologie i drukarki 3D pod względem szeregu przydatnych kryteriów.
Co znajdę w poradniku?
- Opisy cech charakterystycznych technologii druku 3D.
- Porównanie drukarek 3D różnych producentów według segmentów rynku.
- Porównanie technologii druku 3D.
- Case study zakupu drukarki 3D.
Projekt #2 – Zaślepka z logotypem
Następnie w celu przetestowania możliwości technologii i żywic do druku 3D wykonaliśmy wspólnie z firmą 3DeM testy z użyciem wkładek z żywicy Rigid 10K, które zostały wydrukowane w naszej pracowni.
W projekcie naniesiono kilka modyfikacji:
- Dla zwiększenie skomplikowania geometrii formy dodaliśmy napis – logotyp CADXPERT.
- Dodanie kanałów odpowietrzających o przekroju 1 × 0,05 mm w celu zniwelowania wad – przypaleń wyprasek w poprzedniej formie z żywicy High Temp.
- Dodanie pochylenia 2,5 stopnia wewnątrz kanałów dla lepszego i łatwiejszego usuwania wypraski z formy oraz dla wydłużenia żywotności formy.
PARAMETRY WTRYSKU
Materiał wkładki — żywica Formlabs Rigid 10K
Materiał wtrysku — TPE
Siła zwarcia formy — ok. 10-15 T
Ciśnienie wtrysku — ok. 35-40 bar
Temperatura wtrysku — 140 °C
Liczba wtrysków — 30 sztuk
Czas chłodzenia wypraski w formie po wtrysku — ok. 10 sekund (przy każdorazowym chłodzeniu gniazda sprężonym powietrzem 6-8 bar przez kilka sekund)
Całkowity czas cyklu (przy chłodzeniu gniazda sprężonym powietrzem i wyjmowaniu wypraski ręcznie z formy) — ok. 30-40 sekund.

Proces produkcji wkładki z użyciem technologii druku 3D – SLA
- Zaprojektowanie formy
- Drukowanie 3D
- Płukanie wydruku w IPA w urządzeniu Form Wash
- Utwardzanie wydruku w Form Cure
- Obróbka narzędziowa – szlifowanie do uzyskania docelowych wymiarów zewnętrznych w celu ciasnego pasowania w metalowej oprawie
- Precyzyjne rozwiercanie otworów
- Mocowanie wkładki do oprawy i montaż formy na wtryskarce
- Formowanie wtryskowe
Porównanie kosztów
Ze względu na stopień skomplikowania geometrii – ostre kąty w literach logotypu oraz niewielkie wymiary wkładki (70×35×10,1 mm) jedyną możliwą technologią produkcji byłoby elektrodrążenie. Koszt wykonania wkładki przez zewnętrznego dostawcę techniką elektrodrążenia wynosi ok. 13 – 15 tys. zł. i trwa od 2 do 3 tygodni. Drukowanie 3D na własnej drukarce z materiału Rigid 10K to koszt ok. 30 zł.. Proces druku tego typu wkładki trwa 4 godz. Do czego należy jeszcze doliczyć czas potrzebny na obróbkę wydruku i montaż do oprawy – co łącznie daje od 1 do 2 dni roboczych.
Technologia | Czas wykonania | Koszt |
Elektrodrążenie | 2-3 tygodnie | 13 000 – 15 000 PLN |
Drukowanie 3D | 1-2 dni | 30 PLN |
Druk 3D w formowaniu wtryskowym
Technologia druku 3D umożliwia szybkie i ekonomiczne tworzenie w pełni funkcjonalnych wkładek do form wtryskowych, przyspieszając proces prototypowania i produkcji krótkich serii.
Dzięki zastosowaniu innowacyjnych materiałów i precyzyjnych systemów drukujących, można uzyskać wysokojakościowe elementy odporne na wysokie temperatury i ciśnienie.
Rozwiązanie to zmniejsza koszty oraz skraca czas wdrożenia produktu na rynek, co przekłada się na większą konkurencyjność firm.
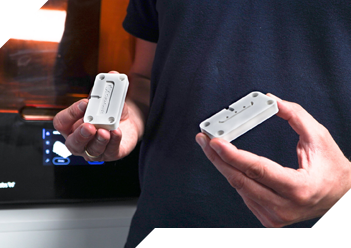
Prześlij formularz, nasz konsultant skontaktuje się z tobą w ciągu 30 minut
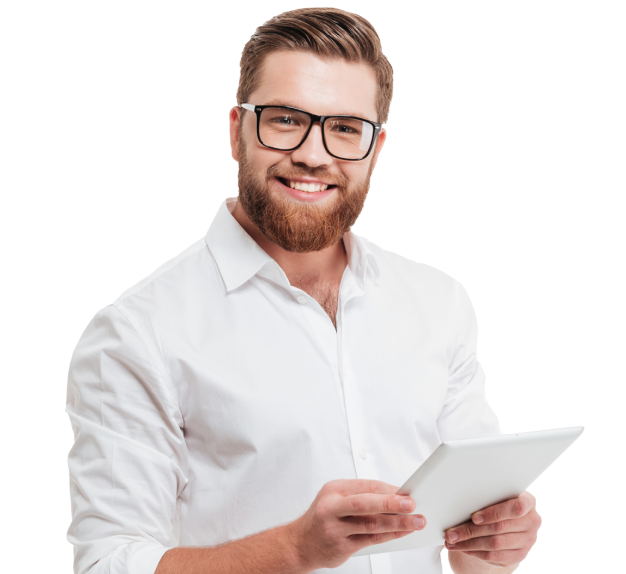